Viscose-fabrics for fibre reinforced wood composites
SUPERVISOR: Ulrich MÜLLER
PROJECT ASSIGNED TO: Bernhard UNGERER
Background:
The wood industry and in particular the segment of engineered wood products is currently experiencing a global rise in demand. Taking for instance the building sector, trends towards prefabricated housing solutions have significantly pushed the production of cross laminated timber (CLT) or glued laminated timber (GLT). Due to this economic potential, countries formerly exporting raw materials start building their own capacities for industrial processing of wood.
These upcoming players stand in competition with traditional regions of wood technology such as Central Europe, Scandinavia, or Northern America. Instead of enduring critical tendencies, however, towards a degradation of price levels, more emphasis should be placed on the development of novel wood and fibre-based products as well as opening new sales markets. Recently the automotive industry appears to be a promising industrial sector for the assessment and implementation of innovative renewables-based material solutions. As a subproject of the Austrian Biorefinery Center – Tulln (ABCT) this dissertation holds tight connections to the project WoodC.A.R, a cooperation between BOKU, TU Graz, KFU, and the research centers Virtual Vehicle and W.E.I.Z., helping to ensure an extensive collaboration with various industrial partners from the automotive and wood industry.
Idea:
The dissertation is about the fabrication and characterization of composite materials combining wood and cellulose fibres, focusing on viscose. By this, cellulose fibre reinforcement prototypes for different use cases and structural elements will be developed which in terms of mechanical behaviour are superior to entirely wooden systems as well as competing with current plastic- and metal-based materials on the market. High performance viscose shall serve as substitute for glass or carbon fibre reinforcements which currently dominate the field of fibre-reinforced composites.
Outline:
The conduction of the project will follow a bottom-up approach as illustrated in figure 1. Within a first stage the viscose fibres used as reinforcement are analysed with respect to their mechanical properties. Subsequently the bonding between fibre and matrix (see figure 2), as well as fibre-matrix-wood, respectively, is investigated in order to determine appropriate matrix/adhesive systems depending on its applications. The data generated from fibre and fibre-matrix testing will be implemented in models for vehicle components in order to validate its feasibility. Eventually entire component will be crafted and by this the potential of high performance wood-cellulose fibre composites shall be indentified.
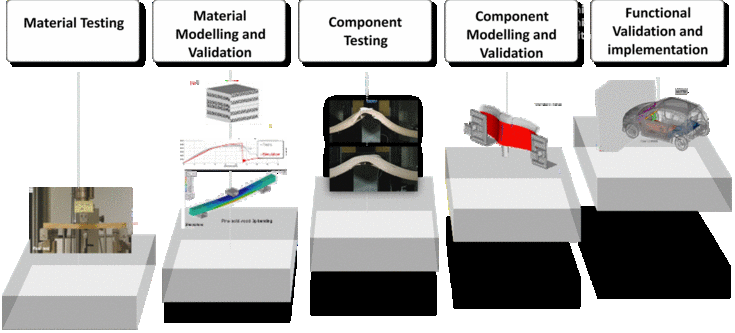
Fig. 1: concept for design steps which help to optimize the predictability of components and minimize the material input
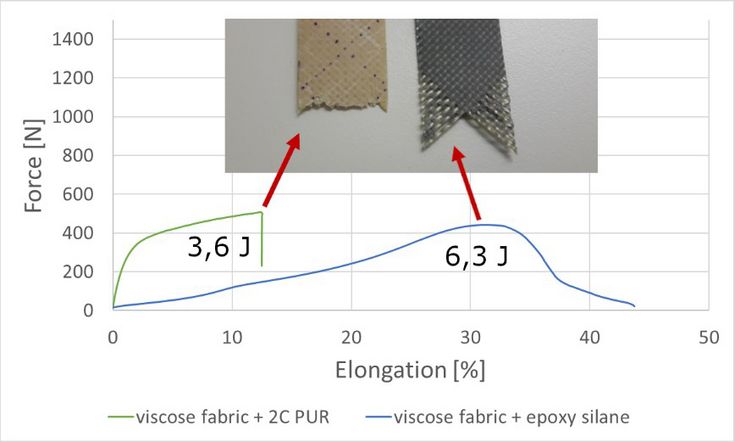
Fig. 2: comparison of tensile test specimen from two fibre-matrix combinations; differing fracture pattern of polyurethane (left/green) and epoxy silane (right/blue) including fracture energy (in joule)