Development of control concepts and integrated solutions in a fully continuous and automated End-to-End manufacturing process platform of biopharmaceuticals focused on the upstream part
SUPERVISOR: Alois JUNGBAUER
PROJECT ASSIGNED TO: Magdalena PAPPENREITER
The state-of-the-art production process of monoclonal antibodies is batch-based. After the cultivation of mammalian cells in fed-batch mode, the primary recovery is carried out by individual unit operations for concentration, purification or polishing of a product. Currently, the biopharmaceutical industry sector is investing great efforts to establish continuous and integrated manufacturing processes. A continuous process is ideally in the so-called "state of control" and offers many advantages over batch-based processes, such as stable operation and product quality at high cell densities, reduction of process dimensions to a factor of 10 to 20 and elimination of unproductive downtime. By using end-to-end continuous bio manufacturing, the cost of goods can even be reduced up to a certain amount.
This PhD thesis is part of a research project funded by Bilfinger Industrietechnik Salzburg GmbH and the Austrian Research Promotion Agency (FFG) to establish a fully automated, integrated and continuous end-to-end platform process skid for the production of biopharmaceuticals. Herein, a continuous process will be established in three unit operations. The prototype starts with a perfusion process, separation with different cell retention systems, capturing by precipitation, polishing, which leads to an end product of monoclonal antibodies in a tightly controlled process.
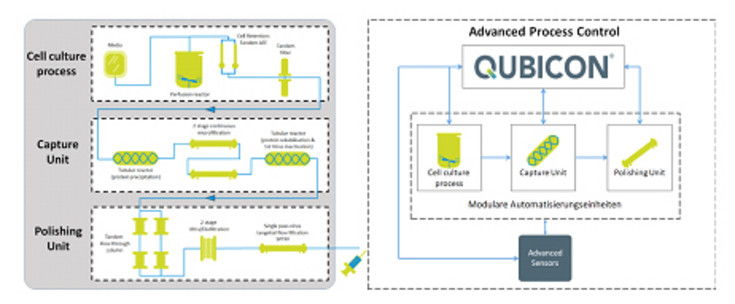
During this work, attention should be drawn to more advanced control strategies in the cell culture unit, where the entire process is controlled, in order to enable even higher potentials in continuous production. Using a recombinant CHO cell line, a perfusion process with different cell retention systems built up in laboratory experiments will be established, scaled up and evaluated for its feasibility for (pilot) scale production. Certain strategies to improve cell performance in terms of media and process design (DoE) during the long-term perfusion mode should be tested. By implementing the designed control concepts, a final stress and robustness test of the entire end-to-end prototype in a fully continuous and automated manufacturing process will demonstrate its applicability and the proof of concept of this study.