Economic and ecological evaluation of new processing schemes for the enzymatic treatment of non-recycled plastic fractions
SUPERVISOR: Gerald STRIEDNER
PROJECT ASSIGNED TO: Tommaso DE SANTIS
Global plastic waste production is estimated to be 27.1 million tons per year 1. About two thirds of plastic waste are landfilled or incinerated and only 31.1% is recycled (Figure 1). Plastic waste is linked to 6.7 million tons of CO2 emission per year while the economic impact of plastic waste management accounts for over 19.3 billion Euros per year 2.
Enzymatic plastic depolymerization (Figure 2) has emerged in recent years as a new promising technology to target the plastic waste fractions (e.g. PET trays) which are currently not recycled. Despite the discovery of several plastic-degrading enzymes 3 and the proof of concept at a pilot scale of the process 4, multiple challenges are found ahead to make the enzymatic recycling of plastic a commercially competitive technology. One of the main obstacles is the scalability of the process and the costs associated with it. In order to deal with a significant percentage of the European plastic waste volume, an enormous quantity of enzymes will need to be produced. As new and more efficient enzymes are isolated and engineered to increase activity and stability, the enzymatic activity will increase hence lowering the enzyme dosage per unit of plastic. Other strategies to scale up effectively are the adoption of continuous in-situ enzyme production and the optimization of the depolymerization process. Enzyme recovery can also help to reduce the costs of the overall recycling process.
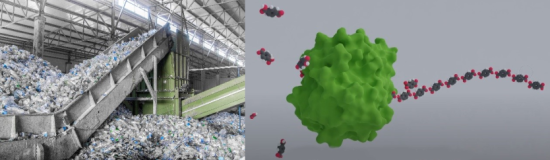
Figure 1 (left) and 2 (right)
In order to assess the readiness of this new technology and the feasibility at industrial scale, a techno-economic analysis (TEA) of both the recycling schemes and the relative enzyme production will be performed.
The TEA is meant to estimate the overall costs and profitability of a large-scale recycling plant as well as the main environmental metrics (i.e. water, energy consumption, CO2 eq. emission). These output numbers will then be compared with the status quo of the plastic recycling industry in order to understand the advantages and disadvantages of the proposed solution. Multiple scenarios and process improvements will be evaluated with the aim of designing the best possible processing schemes and relative setup. A fundamental parameter that will be calculated is the “green premium” which is defined as the additional cost of choosing a clean technology over one that emits a greater amount of greenhouse gases (Gates, 2020). The lower the green premium, the more likely is that a green technology will replace traditional carbon emitting ones, therefore it represents a key number to define the readiness of the solution under examination.
The doctoral research is part of the EU funded ENZYCLE project (H2020-BBI-JTI-2019) involving 13 industrial and academic stakeholders. More info at www.enzycle.eu
1. PlasticsEurope. An analysis of European plastics production, demand and waste data. Plast - Facts 2017. Published online 2018:44.
2. Enzycle consortium. www.encycle.eu. Published 2020. Accessed February 5, 2021. www.enzycle.eu
3. Kawai F, Kawabata T, Oda M. Current State and Perspectives Related to the Polyethylene Terephthalate Hydrolases Available for Biorecycling. ACS Sustain Chem Eng. 2020;8(24):8894-8908. doi:10.1021/acssuschemeng.0c01638
4. Tournier V, Topham CM, Gilles A, et al. An engineered PET depolymerase to break down and recycle plastic bottles. Nature. 2020;580(7802):216-219. doi:10.1038/s41586-020-2149-4