Fed-batch and continuous production of PET degrading enzymes in E.coli
SUPERVISOR: Gerald STRIEDNER
PROJECT ASSIGNED TO: Lisa FOHLER
The global plastic production increases exponentially, with an estimated 448 million tonnes manufactured in 2015, about 200 times more than in 1950 [1] and only 9 % of all plastic waste is recycled [2]. PET, being the largest fraction of all produced plastics, is mainly recycled via thermo-mechanical means, resulting in a loss of mechanical stability. However, enzyme-driven depolymerization of PET represents an environmentally friendly option for value-preserving recycling, which could drastically increase the percentage of recyclable PET waste.
The key to this recycling approach is the availability of sufficient amounts of thermostable, PET-degrading enzymes, which implies extremely high yield and cost efficiency requirements on the enzyme production processes used. The quantities of enzymes referred to here, far exceed the quantities of recombinantly produced proteins used in other applications. Thus, we postulate that the required efficiency can only be achieved with continuous production processes and that the problem of genetic instability of production hosts can be circumvented with the help of two-stage chemostat processes in combination with growth-decoupled expression systems.
The first task of this thesis is the generation of a set of production clones, as well as the identification and selection of the best performing expression system. A growth-decoupled E. coli strain will serve as expression host, and different enzyme candidates will be combined with a variety of periplasmic leader sequences. µ-bioreactor cultures will be used for screening and clone selection and with the selected production clone a conventional fed-batch process using model-based design of experiments will be developed. This optimized mode will be the standard process to serve as a benchmark, which the continuous process must exceed. Also, the basic information on the expression behavior gathered in the mDOE will be essential for setting up the continuous enzyme production.
The main task of this work is to set up a 2-stage continuous production process in chemostat mode (Fig.1). The first reactor (R1) will be used to produce biomass which is then transferred to the second reactor (R2) the production vessel, where enzyme production is induced. In addition to conventional optimization parameters such as cultivation temperature, cell densities, and induction strategies, the variation of vessel volumes, dilution rates, and feed-bleed rates are available for the identification of optimal production conditions in this system. In addition to a comprehensive evaluation of the continuous process in comparison to the standard process, an evaluation and fine-tuning of the operational processes and automation approaches in the continuous process is also planned.
The doctoral research is part of the EU funded ENZYCLE project (H2020-BBI-JTI-2019) involving 13 industrial and academic stakeholders. More info at www.enzycle.eu
References:
[1] “Plastic pollution facts and information.” [Online]. Available: www.nationalgeographic.com/environment/article/plastic-pollution. [Accessed: 03-Feb-2022].
[2] R. Geyer, J. R. Jambeck, and K. L. Law, “Production, use, and fate of all plastics ever made,” Sci. Adv., vol. 3, no. 7, pp. 19–24, 2017.
[3] V. Tournier et al., “An engineered PET depolymerase to break down and recycle plastic bottles,” Nature, vol. 580, no. 7802, pp. 216–219, 2020.
[4] J. Kopp, C. Slouka, O. Spadiut, and C. Herwig, “The Rocky Road From Fed-Batch to Continuous Processing With E. coli,” Front. Bioeng. Biotechnol., vol. 7, no. November, pp. 1–16, 2019.
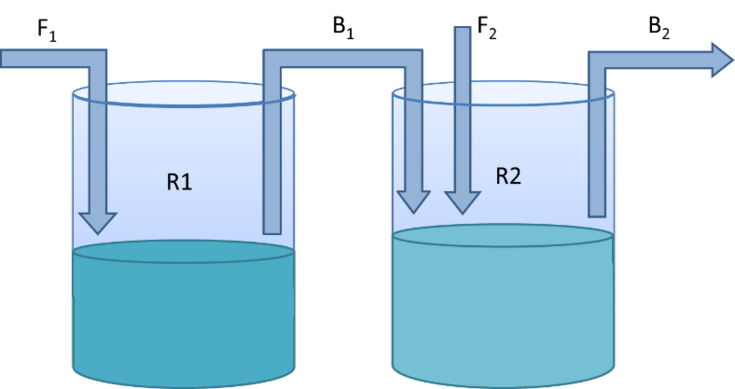
Figure 1: Two-stage continuous production process with R1 and R2 as reactors, F1 and F2 as feed streams and B1 and B2 as bleed streams